Essential Pipe Welding Assessment Tips for High Quality Assurance
How can one assure the quality of these welds that link the pipeline sections? By recognizing the necessary pipe welding inspection pointers, experts can avert possible hazards, decrease pricey repair services, and promote the dependability of these important infrastructures.

Relevance of Welding Inspection
Welding assessment plays a vital function in ensuring the architectural integrity and safety of pipe systems. By carefully examining welds, examiners can determine any kind of flaws or blemishes that might jeopardize the stability of the pipe. These examinations are essential for stopping leakages, ruptures, and various other possibly catastrophic failings that could result in ecological damages, monetary losses, and even death.
The relevance of welding examination can not be overemphasized, as the quality of welds straight influences the general efficiency and durability of the pipeline. With non-destructive screening approaches such as visual evaluation, ultrasonic screening, radiography, and magnetic bit screening, examiners can discover defects that may not be noticeable to the naked eye. By recognizing and attending to these concerns early, welding inspection assists to make sure that pipelines fulfill market requirements and regulative demands.
Inevitably, welding assessment is a critical facet of quality assurance in pipeline maintenance, construction, and repair work (Pipeline Welding Inspection). By upholding rigorous assessment requirements, industry specialists can reduce risks and support the security and dependability of pipeline systems
Usual Welding Flaws
Among the challenges faced in pipe welding, common defects can dramatically influence the architectural integrity and performance of the bonded joints. Some of the most widespread welding flaws include lack of fusion, porosity, splits, incomplete penetration, and imbalance. Absence of fusion occurs when there is insufficient bonding between the weld metal and the base steel, bring about a weakened joint. Porosity, defined by gas pockets within the weld, can reduce the strength and make the weld prone to rust. Fractures in the weld can propagate over time, endangering the structural integrity of the pipeline. Incomplete penetration happens when the weld metal does not fully penetrate the joint, resulting in a weak bond. Imbalance, where the weld grain is not correctly centered, can cause stress concentration factors and potential failing. Spotting and resolving these typical problems with comprehensive assessment and quality assurance his explanation processes are essential for making sure the integrity and security of pipeline welds.
Assessment Strategies for Pipes
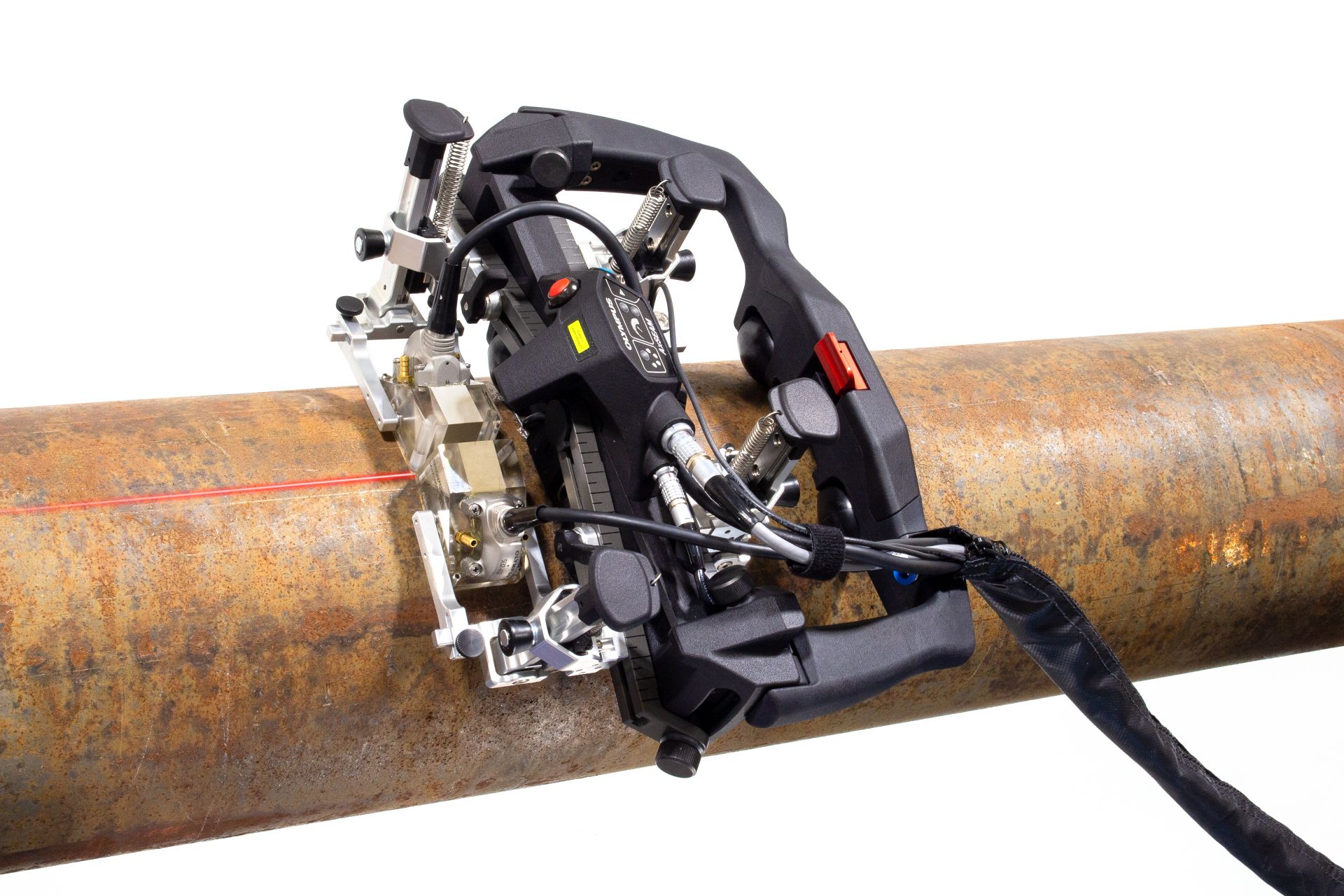

Non-destructive testing (NDT) techniques such as radiographic screening, ultrasonic testing, magnetic particle testing, and fluid penetrant testing are generally used in pipeline welding evaluation. Visual assessment is likewise crucial in pipe welding to identify any type of noticeable defects or stoppages. best site Furthermore, computerized inspection methods making use of advanced innovations like drones and robotics are increasingly being utilized to boost the efficiency and accuracy of pipe evaluations.
Making Sure Quality Assurance Specifications
To maintain rigid top quality guarantee criteria in pipeline construction, careful adherence to established market procedures and guidelines is site web crucial. Quality guarantee in welding processes requires a comprehensive method encompassing numerous phases of pipe construction. Carrying out a robust quality management system that includes regular audits and reviews can even more boost the general high quality assurance standards in pipeline welding.
Protecting Against Costly Repair Work
Provided the crucial relevance of keeping rigorous quality assurance criteria in pipeline construction, a positive method to avoiding costly repairs is essential. Normal maintenance checks and tracking of ecological factors that can influence the stability of the pipeline are also vital in avoiding expensive repair services. By spending in preventative procedures and focusing on quality assurance at every stage of the pipeline welding process, business can reduce the danger of pricey repair work and make sure the long-lasting dependability of their framework.
Final Thought
In conclusion, adherence to correct welding assessment techniques is necessary for making certain the quality and honesty of pipelines. By determining common welding flaws and implementing extensive evaluation procedures, pricey fixings can be prevented, and quality control criteria can be fulfilled - Pipeline Welding Inspection. It is important for pipe welders to focus on examination procedures to keep the safety and dependability of the facilities they are servicing
The value of welding assessment can not be overstated, as the quality of welds straight influences the total efficiency and durability of the pipeline. Non-destructive testing (NDT) techniques such as radiographic screening, ultrasonic screening, magnetic fragment testing, and liquid penetrant screening are commonly used in pipe welding assessment. Aesthetic examination is additionally essential in pipeline welding to identify any kind of visible defects or suspensions. Additionally, automated examination strategies utilizing advanced modern technologies like robotics and drones are progressively being used to boost the effectiveness and precision of pipeline evaluations.In verdict, adherence to correct welding examination techniques is important for making sure the quality and stability of pipelines.